Flash Dryer For Lithium Iron Phosphate
With the rapid development of the new energy vehicle industry, lithium iron phosphate is widely used in power lithium batteries due to its outstanding advantages such as high voltage, large capacity, high energy density, long cycle life, low self-discharge rate, no memory effect and green environmental protection.
In view of the relevant characteristics of lithium iron phosphate, Griffin Machinery has developed equipment that can be used for lithium iron phosphate drying.
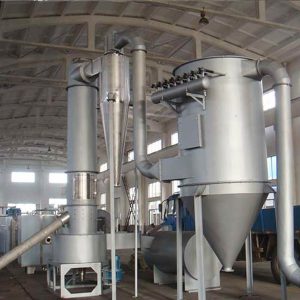
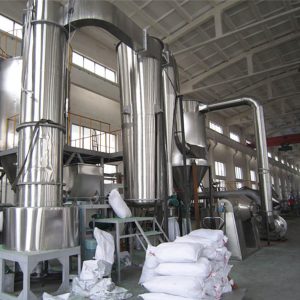
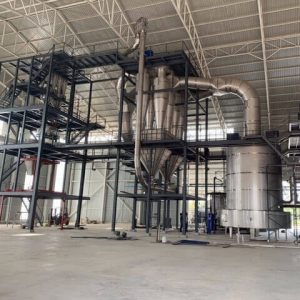

Lithium iron phosphate flash dryer is a new type of high-efficiency fluidized bed drying equipment developed by our company to overcome the low efficiency and high consumption of static drying. In the design process of this machine, it fully combines the characteristics of ordinary fluid drying such as airflow drying and avoids weaknesses.
Main features of our lithium iron phosphate dryer:
- The bottom of the lithium iron phosphate dryer is designed with a conical section, which establishes a velocity gradient of the air, which gradually slows down from the bottom to the top, and finally forms a certain axial velocity. Under the dual action of rotating airflow and stirring and crushing, the gas-solid contact of large particles at the bottom is promoted, and drying is accelerated.
- The hot air enters the bottom of the dryer by rotating at high speed from the annular bottom gap. The bottom gap is set on the inverted cone of the gas collection chamber, and the stirring blade can be extended to the bottom of the gas collection chamber to prevent the rabbit material from entering the gas collection chamber and seal the air inlet annular gap, resulting in a dead angle.
- The outer wall of the gas collecting chamber is a helical line, which gradually becomes smaller due to the section of the inner cavity, which promotes the rotation of the hot air and enters along the annular bottom gap, eliminating the dead angle at the bottom, and also adopts the double air channel technology. Same effect.
- Set up a grading ring, with which the particle size of the finished material can be controlled.
- The double-screw feeding method is adopted to make the high-viscosity paste-like and filter-cake-like materials enter the dryer evenly, and at the same time, it has a certain crushing effect on the larger particle materials.
- A variety of feeding devices are available for selection, the feeding is continuous and stable, and there is no bridging phenomenon in the process.
- A special cooling device is installed at the bottom of the dryer to avoid the deterioration of materials in the high temperature area at the bottom.
Ternary Material Tray Dryer
From 2017 to the present, the upgrading of the power battery system will be prominent in the field of ternary lithium batteries.
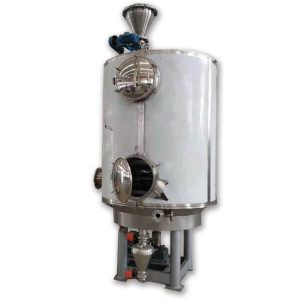
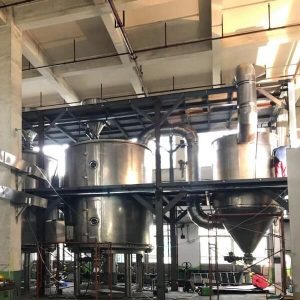
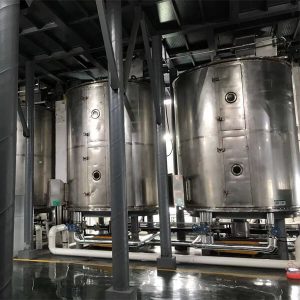
The traditional ternary material drying system uses a hot air circulation oven, and the ternary material is placed inside the oven to be heated and dried until the drying is qualified, and then a batch of drying is completed by manual unloading.
Although this drying method has low equipment cost, the labor intensity of workers is high, the floor space is large, the drying time is long, and the working environment is poor, which cannot meet the needs of mass production.
According to the characteristics of ternary materials, our company's technicians have developed a new type of special tray dryer for ternary materials which is a new type of conduction drying equipment, which is simple in configuration, does not need the cyclone dust collector that must be configured for airflow drying, and does not use hot air as a heating medium. Therefore, product loss due to poor separation of hot air and dust will not occur.
The Structur of Ternary Material Tray Drying
It consists of a drying tray, a rake arm, several rake blades mounted on the rake arm, a main shaft, a transmission device, a casing, etc.
Working Principle
The heating medium is passed into the hollow drying tray, the drying tray is arranged in a horizontal layer in the dryer, the drying tray is stationary, the material is pushed and moved by the rakes on the surface of the tray, and is heated by the drying tray during the movement for heat transfer. The drying operation is completed with high quality, and the entire drying process is closed.
Determine the number of drying tray layers (drying area) according to the output, properties, initial and final moisture content of the material to be dried.
Main Features of Ternary Battery Material Dryer:
- Continuous operation, high thermal efficiency: The disc continuous dryer is dried by conduction heat transfer. During the drying process, only a very small amount (or no) of air is introduced into the dryer, and the amount of exhaust gas carried is very small, so its thermal efficiency can reach 65%. %above.
- Low power consumption and low noise: Due to the thin material layer and low spindle speed in the drying process, the power required by the material conveying system is small, and the power consumption is very small. The power consumption of the complete drying device is only that of the convection heat transfer device. 1/5~1/7, and the noise is very small.
- The material is heated evenly and the drying time is short: during the drying process, the material rolls forward along the Archimedes spiral trajectory in the drying tray, and the distance traveled by the material is 5 times the radius of the drying tray and falls layer by layer, so the material is heated in contact with each other. The plate time is basically the same, and the heating is very uniform.
- Small material loss and good environmental protection: During the drying process, the material enters and exits from the top, and the material distribution is also wet on the top and dry on the bottom, and the drying tail gas flow rate is extremely low (about 0.1m/s), so it is difficult for the material dust to float to the equipment. The top will not be entrained and discharged by exhaust gas, not only will not lose materials, but also will not pollute the environment.
- The equipment is closed and continuously operated, and the labor intensity of workers is low.
- Easy installation and small footprint: Due to the layered arrangement and vertical installation of the drying tray, even if the drying area is large, the footprint is small.
- Energy saving: The drying medium can use the waste heat steam generated by the boiler, thus saving a lot of coal combustion.
- Stable product quality: Due to the continuous drying method of disc type, the material is heated evenly, and the product quality can be guaranteed.
Cobalt Tetroxide Disc Dryer
The cobalt tetroxide powder produced by the cobalt tetroxide continuous disc dryer has high purity, good physical properties and electrochemical properties, and the disc dryer is continuously dried, occupies a small area and is easy to operate.
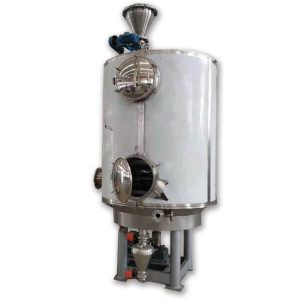
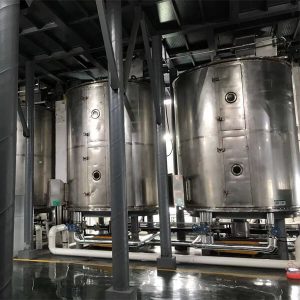
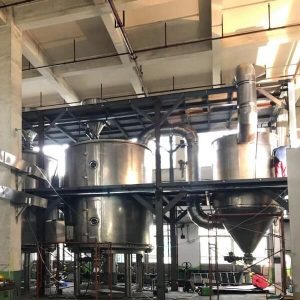
Cobalt tetroxide (Co3O4) is a functional material with a special structure, which is mainly used in the preparation of lithium cobalt oxide, a positive electrode material for lithium-ion batteries. Cobalt tetroxide used in batteries requires very high purity.
Working Principle of Cobalt Tetroxide Drying Equipment
The cobalt tetroxide wet material is continuously fed into the first layer of the disc dryer through the feeder, and falls down layer by layer under the action of the continuous rotation of the rake arm. The heating medium (water, heat transfer oil, etc.) Cobalt tetroxide completes the heat and mass transfer process in the flow process to achieve the purpose of drying, and the dried material is discharged from the discharge port after cooling.
According to product performance, drying requirements and processing capacity, the cobalt tetroxide disc dryer adopts a series of measures such as the stepless speed regulation of the main shaft, the manual adjustment of the disc feeder to adjust the height of the sleeve, the control of the temperature distribution of each layer of the heating plate, and the cooling and cooling in the final stage. Give full play to the superior performance of the continuous disc dryer.